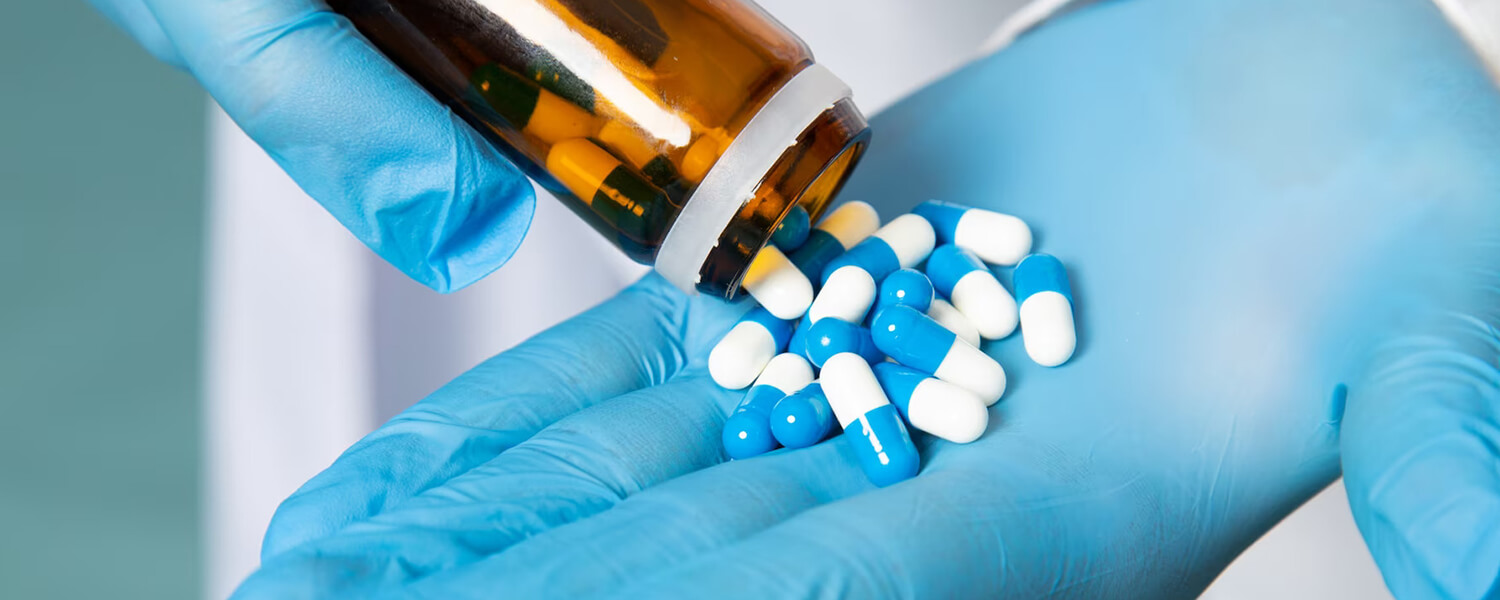
Formulations
Micro Labs stepped into the pharmaceutical arena with a handful of medicines in niche healthcare segments like antibacterial compounds, antiseptics, and vitamins. Today, under the portfolio of Mr. Dilip Surana and Mr. Anand Surana, Micro Labs has evolved into a diversified pharmaceuticals manufacturing advanced formulations in a wide range of products, from oral solids to injectables, and are ranked 18th on sales among the organized sector in the Pharmaceutical Industry.
We are operating 14 world-class plants that boast of having rich R&D facilities that have led to the development of scientific formulations in the manufacturing of pharmaceutical medicines in both penicillin and non-penicillin categories.
Our formulation approach comprises of the following technologies:
Mini Tablets:
With a defined diameter of 2-3 mm, this particular formulation approach provides the following advantages:
- Uniform release kinetics reducing sudden concentration of blood
- Reduces risk of local irritation as they spread throughout the GI tract
- Desired release profile with variations on the coating concentrations on multiple units
Fluid Bed Granulation:
A continuous process involving complete granulation process in one equipment providing the following advantages:
- Resulting granules are lighter and porous in nature
- Granules of uniform sizes are obtained from the process, reducing time spent for sizing or milling
Wurster Coating:
This process allows for precise application of a coating that offers several benefits for modified release dosage forms onto particulate materials such as powders, crystals, or granules, and other solid ingredients.
Tangential Spray Technology:
This spray process prevents agglomerations and provides a coat of comparable quality and uniformity with a higher separation force.
Extrusion Spheronization:
This process plays a key role in minimum variability of the drug release by producing spheroids with high loading capacity of active ingredients which can be filled in capsules.
Hot Melt Extrusion:
Without the need for adding water or any other solvent, this is an efficient process that we follow to minimize prolonged drying stages.
MUPS Compression Machine :
We achieve a uniform drug release phenomenon and reduce the risk of dose dumping through this formulation process.
Laser Drilling :
Also known as Osmotic-controlled release oral delivery system, we use this formulation technology in the preparation of zero order drug release medicines.